Offset prints for true, bright and clear colors are due to the quality of the ink system used. The most basic offset ink system is CMYK for all different types of printers and printing media.
Ink system used in offset printing
Offset printing uses process colors or four colors known as CMYK.
- C stands for Cyan (a color in the blue/green spectrum),
- M stands for Magenta (a color in the middle of the red/blue spectrum),
- Y stands for “Yellow”
- K stands for Key (black film).
From these 4 primary colors, the printer uses mixing techniques in certain proportions to create the desired color, true to the original color.
This 4-color system gives bold, bright, clear colors, suitable for prints that need these standards. However, its colors are not as faithful as the Pantone color system used in digital printing.
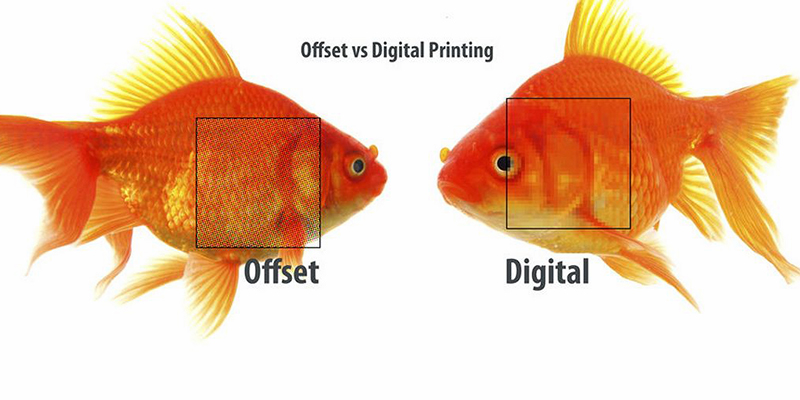
Therefore, when prints need high visibility, digital printing should be used. As for advertising printing, leaflet printing, book covers needing bright, sharp and vivid colors, Offset printing with CMYK color system is the most suitable choice.
CMYK color ink is very suitable for printing product labels and decals because the ink gives vivid, vibrant colors, highlighting images, writing, logos, contributing to much better brand recognition. Inks are used to:
- Print decal paper
- Print plastic decals
Type of ink used in offset printing
Offset printing uses oil-based inks developed by Offset printing from lithography, which applies the repulsion of oil and water. During Offset printing, water will be applied to the entire surface of the printing plate. At the printing plate, water is absorbed at the places where there is no image to be printed. Then, oil-based ink is provided, it will stick to the part of the image to be printed and be pushed out of the places where there is no image. The photo needs to be printed because water does not absorb oil. In addition, Offset printers can use UV inks when UV drying is required to shorten the ink drying time.
Offset printing inks have a basic composition including: Piping (color and filler), film forming agent – bonding agent and additives (drying agent, stickiness modifier, modifier). gloss, anti-fouling agent).
Immediately refer to the printing service using Offset technology in Malu to better understand.
About Pisces
When the ink is affected by physical and chemical factors, the pigment is changed, so the ink color property is determined according to the durability of the ink film.
There are two types of spark plugs: colored flanges and padded flanges. All plugs used in the manufacture of printing inks are not soluble in binders or solvents.
Color flanges:
Color Spanking is a substance added to offset printing ink to adjust the color tone. The quality and quantity of the spigot used determine the color tone or tint, color brightness and saturation or saturation, and the purity of the ink color.
How to prepare colored spark plugs (spindle shaking method): Dyes are not used in the production of printing inks because most of them are water soluble. To use them in the manufacture of printing inks, the dye must be converted to a water-insoluble form by chemical methods (Dye cementation) as follows:
- Dyes together with the carriers or substrates (Substrate) are barium salts, calcium salts easily soluble in water, they react with each other to form a precipitate. Precipitation – the shaking or sparing of the dye to form a colored piston.
- The precipitated spigot is filtered, dried and finely ground. The spigot is prepared by precipitating anionic or cationic organic synthetic dyes with metal salts that readily form a precipitate. For example: Barium Chloride (BaCl2),Calcium Chloride(CaCl2)… Depending on the structure and affinity of organic dyes, chromophores are classified into many different groups such as azo spigots, phthalocyanin spigots.
Color piston rods are now commonly used to produce offset printing inks because they have outstanding advantages such as resistance to alkalis, acids and some insoluble in organic solvents.
When choosing ink, it is important to pay attention to the following important properties of the color piston:
- Shades of colors or tones?
- Color intensity or depth?
- High usage efficiency
- Visibility / Coverage
- Wetting ability with binder molecules: Oil – plastic
- Particle size or fineness
- Light fastness
- Resistance to water, acid, alcohol, alkali, temperature etc.
Padded flanges (White):
The effect of filler in Offset ink:
- Increase the brightness of tones
- Adjust the viscosity
- Limit dust accumulation during printing
- Product cost reduction.
About the film forming agent: (binding agent, varnish, resin oil)
The film forming agent in printing ink is often called a binder. Offset printing requires a good wetting and hydrophobic binder. The main component of the bonding agent is a mixture of oil and resin. Film forming agents include:
Plastics: Natural resins that have been modified, for example: turpentine; synthetic resins, etc. Alkyd resins are used as printing inks, they are soluble in linseed oil and mineral oil. The alkyd resin is modified with linseed oil to form oil-soluble ethers, the gas absorbs oxygen to form a mesh reaction, and the ink film dries.
Modified alkyd resins are increasingly used to produce glossy, fast-drying offset inks, because they have the following outstanding advantages:
- High scratch resistance printing ink film
- Form a glossy ink film
- Matching the friction resistance of Offset printing ink
- Fast drying time if using binder: alkyd resin – linseed oil.
- Diluent – Oil solvent with high boiling point
Oil: For offset printing ink, the oil component in the binding agent is mainly linseed oil. For offset printing ink roll paper, the oil component in the binding agent is mainly mineral oil. The binder composition in offset printing ink is about 55 to 75%.
- Flax oil: Belongs to the type of vegetable dry oil. The unsaturated fatty acids present in flax oil are palmitic acid and stearic acid, which account for 4.5 to 6%. The physical and chemical properties of linseed oil in offset inks depend on the double bond position and the number of carbon atoms in the linoleic acid, linoleic acid and folic acid molecules. These unsaturated fatty acids after printing easily combine with air oxygen by oxidation polymerization, making the ink film dry.
- Mineral Oil (Printing Ink Oil): Mineral oils used in offset printing inks are printed linear hydrocarbons (paraffins and olefins) and cyclic (naphthene or aromatic) hydrocarbons. In offset printing ink, especially roll paper offset ink used to print books, mineral oil nap then is often used more.
- Mineral oil used to produce thermally dry ink is produced separately, refined almost colorless, odorless, boiling point from 240 degrees Celsius to 270 degrees Celsius. For offset printing ink, cold-drying paper rolls and mineral oil newspaper printing ink with boiling temperature from 300oC to 350oC.
- Mineral oil used for offset printing inks has a boiling point of 300 degrees Celsius to 350 degrees Celsius.
The properties and uses of binders can be summarized as follows:
- Forming a protective layer, surrounding the spigot, avoiding mechanical friction when using printed products.
- When the binder is completely dry, the piston is firmly adhered to the surface of the printed material.
- Very finely dispersed spastic seeds in the film-forming agent.
Learn more in the article Composition in Offset Ink .
About additives
Additives added to printing ink usually include:
- Desiccant: Purpose to promote oxidative drying.
- Ink oil: Adjust the viscosity, stickiness, rheological state of printing ink
- Anti-adhesive: Creates a fast drying of the ink film and prevents dirt from the back of the printed sheet.
- Gloss enhancer: Use glossy varnish to increase the gloss of the ink film.
In addition to conventional oil-based inks, in some cases of offset printing using UV drying, special oil-based inks need fast-drying properties under UV rays. UV Offset Printing meets the needs of customers for fast printing and durable map prints. However, the cost of this ink will be higher and the printing price will also increase. Therefore, only when absolutely necessary and printing a moderate amount should be used this way.
Other information about Offset printing that you may be interested in