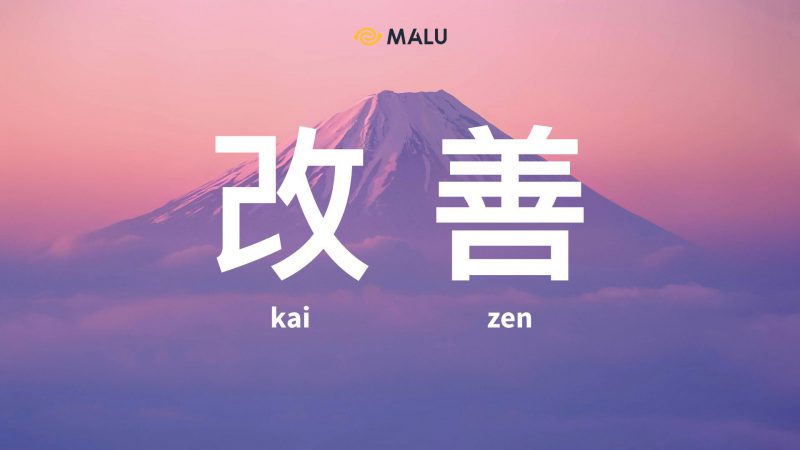
Improving business processes using Kaizen and 5S standards is a way to help organizations reduce costs, shorten cycle times, and improve quality to achieve a systematic, innovative approach. continuous. But how to get the optimal solution that brings the most practical efficiency in corporate governance?
In this article, Malu will discuss Kaizen and 5S which are two methods originating from Japan that are increasingly being used by organizations and businesses to improve business processes and maximize profits. .
>>> What is BSC? Applications of the Balanced Scorecard
What is Kaizen?
Kaizen is the term for an economic method created in Japan after World War II. Kaizen is compounded by the word 改 (“kai”) which means change and the word 善 (“zen”) which means better, i.e. “change for the better” or “continuous improvement”.
This term in English is “ongoing improvement” or “continuous improvement” which means continuous improvement, for the benefit of the group rather than the benefit of individuals. Everyone is encouraged to come up with ideas and suggestions for small improvements on a regular basis.
In Japanese companies, Toyota – a pioneer in using Kaizen or Canon, Honda, employees often make 60 to 70 proposals per year, which are written, shared and implemented. In most cases, this is not the idea for major changes.
The Kaizen method is based on making small changes on a regular basis: consistently improving productivity, safety and efficiency while reducing waste. Kaizen is not limited to a specific field such as production or marketing, but it is widely applied in all companies in many different fields.
Western philosophy can be summed up as “If it ain’t broken, don’t fix it”. The Kaizen philosophy is “Make it better, improve it, even if it’s not broken; because if we don’t, we can’t compete with people who are trying to improve it.” Kaizen includes many well-known Japanese process improvement methods such as: quality circle, process automation, recommendation system, just-in-time delivery, Kanban and 5S.
>>> 10 Business Models For Startups
What is 5S Standard?
5S is a productivity improvement method, which is abbreviated from the first five letters of Japanese words: Seiri, Seiton, Seiso, Seiketsu and Shitsuk e. Methods used to organize an efficient workspace. Let’s learn each letter “S” and determine its meaning.
Seiri – Sort: Keep essential documents in the work area, organize less frequently used items in other storage areas, and remove unnecessary things.
Seiton – Arrangement: The ingredients are arranged in their correct place. Each part should be clearly labeled or demarcated and organized in a way that promotes efficient workflow. Workers do not need to waste time searching for materials.
Seiso – Clean : Clean the workspace and all equipment, and keep it clean and tidy. Daily follow-up cleaning is required to maintain this improvement. A tidy environment will increase work efficiency.
Seiketsu – Standardization: Work practices should be consistent and standardized. Work stations for a particular job need the same setup. All employees doing the same job should be able to work in any station with the same tools in the same location in each station, and everyone needs to know exactly what their responsibilities are.
Shitsuke – Maintain: Once the previous 4s have been established, they become the new way of operating. Businesses need to maintain focus on this new process and not allow superficiality to lead to a return to old ways of doing things. The effect of continuous improvement (Kaizen) helps reduce waste, better quality and faster work time.
How to Apply the Kaizen Method
Kaizen is the method of setting standards and then continuously improving those standards. To support higher standards, Kaizen also involves providing necessary training, documentation and supervision for employees to achieve higher standards and maintain their ability to meet those standards across the board. the base is doing. The cycle of Kaizen activity can be as follows:
- Standardize operations.
- Standardized operational measurement (find cycle times and in-process inventory counts).
- Measurement assessment on request.
- Innovate to meet requirements and increase productivity.
- Standardize new and improved operations.
- Continue the cycle continuously.
The key elements of Kaizen are quality, effort, involvement of all employees, willingness to change and sharing. Kaizen attracts and develops people who are creative and highly productive. The practical results of applying Kaizen are creating a comfortable working environment, motivating them to constantly bring out many innovative initiatives that benefit the company.
The most successful example of applying Kaizen method in business strategy is Toyota. Toyota has about nine factories in North America and earned more than $14 billion in 2006, despite making cars with high-wage American workers; 75% parts, assembly materials are produced here. Meanwhile, American automakers have to move to China and India to save on production costs.
Toyota’s secret here is Kaizen – reducing waste in areas such as inventory, waiting time, transportation, worker travel, worker skills and minimizing production. surplus output. With the Kaizen system, each worker in the factory always does the job easily and simply.
Benefits of the 5S Standard
5S was originally intended for use in the manufacturing process but it also works well in office or administrative environments, even in the healthcare sector to provide patient care. .
The 5S rule is increasingly widely applied and popularized in business process management systems, and has become a core value of enterprises thanks to the following practical benefits:
1. Increase efficiency and productivity
The 5S elements work to keep every aspect of your business organized and running efficiently.
For example, in a retail store, the items at each cashier station have exactly the same label and organization. Anyone can walk in and start working with clients right away.
As a result, cashiers can spend more time working with customers and less time on production tasks.
2. Enhance workplace safety
A clean, well-organized work environment that applies 5S rules will reduce hazards and thereby create a safer workplace. Standard safety first operating procedures require employees to clean up problems immediately, keep aisles clutter-free, and store items in their proper locations.
This is especially important for businesses that comply with Occupational Safety and Health Administration regulations. Good organization, including storing commonly used items close to the work area and in the correct locations helps reduce unnecessary movements, reduce activities that can cause injury.
3. Effective cost control
Implementing a 5S standard system can have significant direct and indirect cost-saving advantages. When your business is organized, better organization reduces storage space requirements. On the other hand, you will minimize the cost of lost or misplaced related inventory.
>>> Tips for managing business expenses
In a manufacturing business, regular preventive maintenance and cleaning procedures make it possible for employees to find and resolve problems with machines and other equipment before problems become more serious. and require costly repairs. Additionally, a safer work environment can reduce health and business insurance costs.
>>> 12 Effective ways to manage inventory and inventory
4. Increase customer satisfaction and employee morale
Everything that happens within the 5S system of rules works to provide value to your customers and increase customer satisfaction. For example, even though your customers might not be interested in hosting cashiers or regular cleaning programs, they will be interested in fast checkout lines and appreciate a clean store. well arranged.
In addition, because commitment to 5S requires massive employee participation, this not only increases employee engagement, but also creates a more pleasant working environment in which employees feel more comfortable. feel more proud of their work.
>>> Examples of Corporate Culture
Recognizing the importance of Kaizen and 5S rules, leaders and managers need to start building strategies and strictly follow the 5S standard Kaizen system to orient management and shape public culture. company and build internal processes for optimal operational efficiency.
Hopefully the above article of Malu has helped you gain more knowledge to apply in your business management!
Learn more about Business , and Marketing at Malu .’s Blog